Piece by piece
This is how I can help.
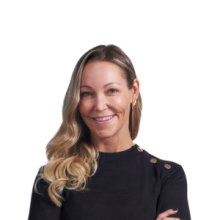
Ashley Conyngham
Director, Marketing and Communications
- I can share your local business news & events
- Promote your tech or manufacturing jobs
- Collaborate with you on your industry event
- Help your business reach new audiences
- Provide communications support for your SME